With the finished product in our hands, it’s difficult to appreciate the man and machine power that goes into making a motherboard. I’m always keen to learn more about how the sausage (or, in this case, silicon) gets made, and MSI was more than happy to sate my curiosity. Following a tour of the company’s factory, dressed in green gowns that definitely made me feel more baker than journalist, I’ve come away with a newfound appreciation for the bedrock of my system and those around the world.
To understand what makes a motherboard, I flew out to Shenzhen, China to meet with MSI. There, I had the pleasure of Ethan Yang’s company, vice president of the MSI Shenzhen. His knowledge of the inner workings of each part of the manufacturing process speaks to his 25 years with the company. Despite the decades of experience behind him, his enthusiasm for improving efficiency and quality remains high, which are both necessary traits when working in the world of PC components.
Welcome to Gargantua
To my welcome surprise, MSI gave me unfettered access to the assembly line, providing plenty of detail about its processes. However, in a bid to protect trade secrets, I’ve obfuscated all screens containing data points at the company’s request.
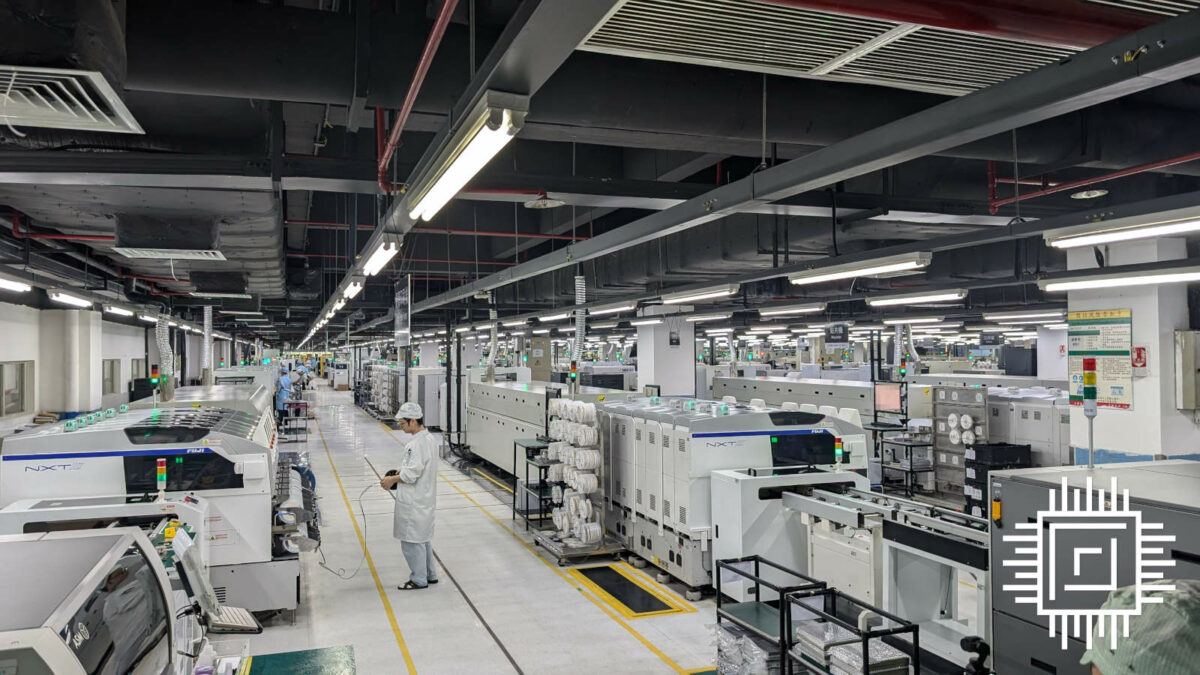
Entering the factory floor, the scale of it all makes it difficult not to feel at least a little overwhelmed. Spread across the room are countless production lines, seemingly go on forever, all servicing the creation of various motherboard models totalling in 1.3-million units per month. Breaking it down, that represents a completed motherboard every two seconds, without pause, all year long. It takes a full minute or so to walk the length of each conveyor belt, but each board will take around 90 minutes to complete its journey from bare PCB to branded package.
If the sheer sight of this operation doesn’t knock you back, the heat and noise of it all will certainly finish the job. As I’ll explore later, this floor contains machines continuously operating at temperatures north of 100°C. Thankfully for me and the manual operators, air conditioning saves us from melting into a proverbial puddle, much as our ears might long for quieter pastures. This is just one floor of a 200,000m² campus, making the entirety of MSI’s operation feel all the more enormous.
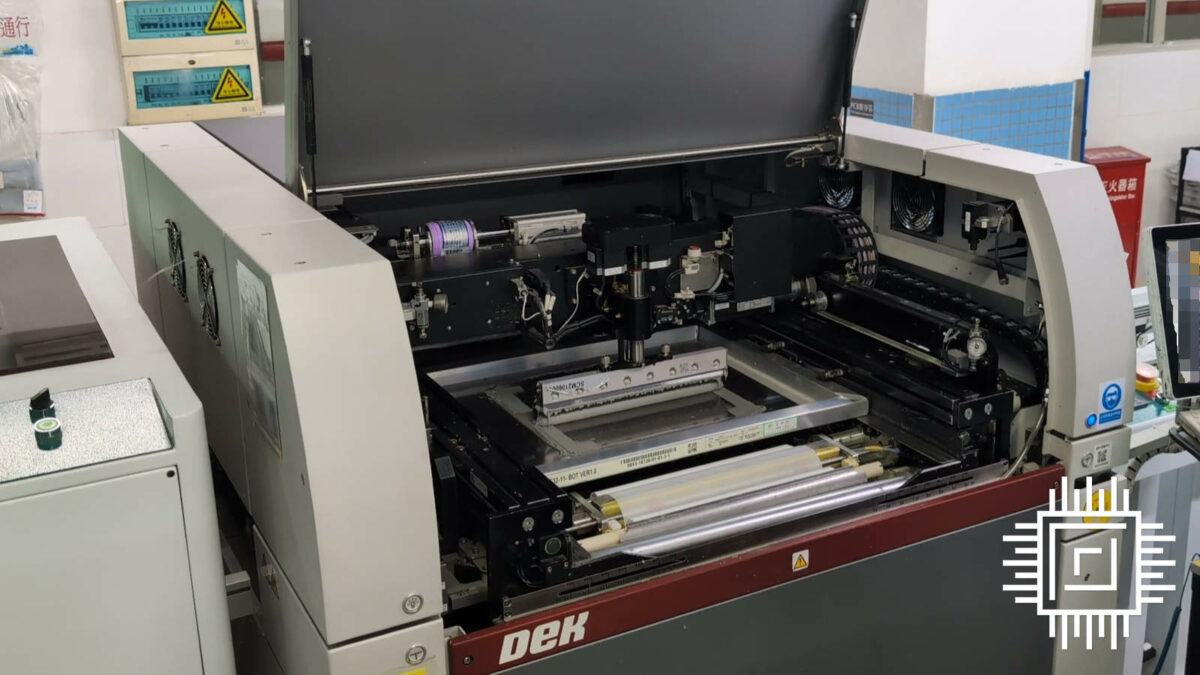
So, it begins
Like most electronics, motherboards begin their life as a naked printed circuit board (PCB) with nary a capacitor or component to speak of. To prepare for these necessary ports and protuberances, the board receives a printing of solder on either side. The underside gets the first treatment, followed by machine application of components before entering a ‘Reflow’. This is essentially an oven that can reach up to 250°C, creating solder joints for components. MSI ramps up the heat up slowly to allow the board to become uniformly heated to avoid potential defects created by differing melting points.
The underside then passes through an Automatic Optical Inspection (AOI), the first of many. This machine uses up to 20 algorithms to analyse the soldering of components, to ensure all is well before the motherboard continues its journey. Yang explains that tolerances are higher than necessary to maintain a high standard of quality, even if this inevitably results in some false positives. All being well, this process then repeats topside.
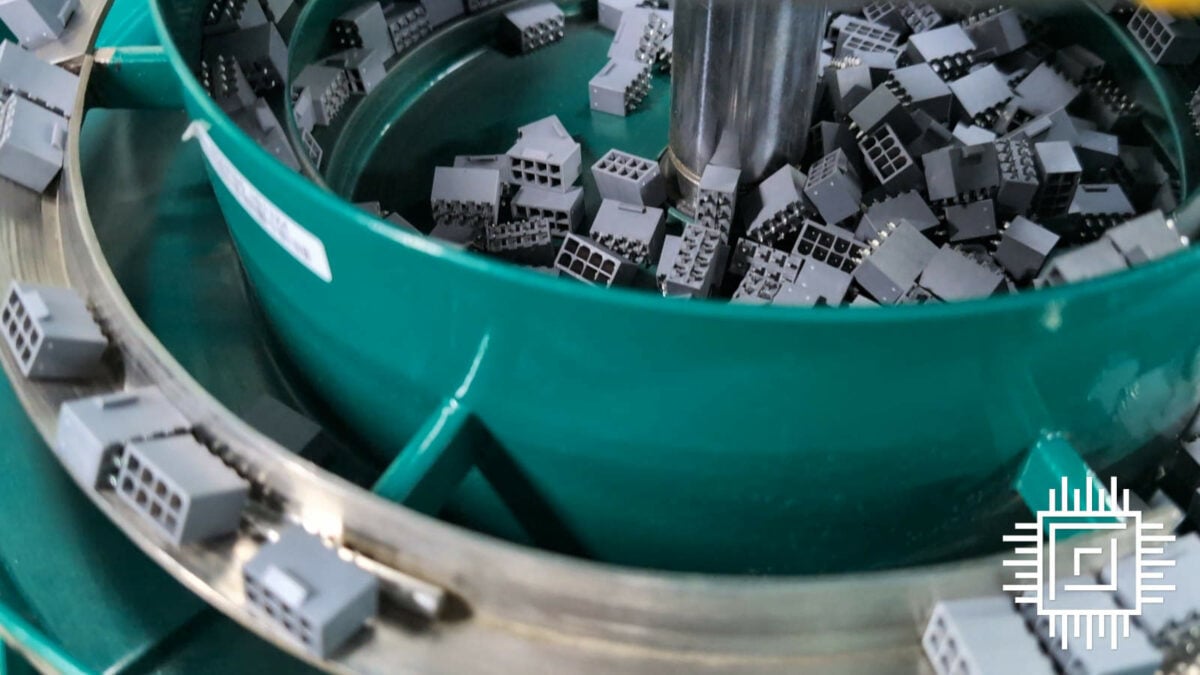
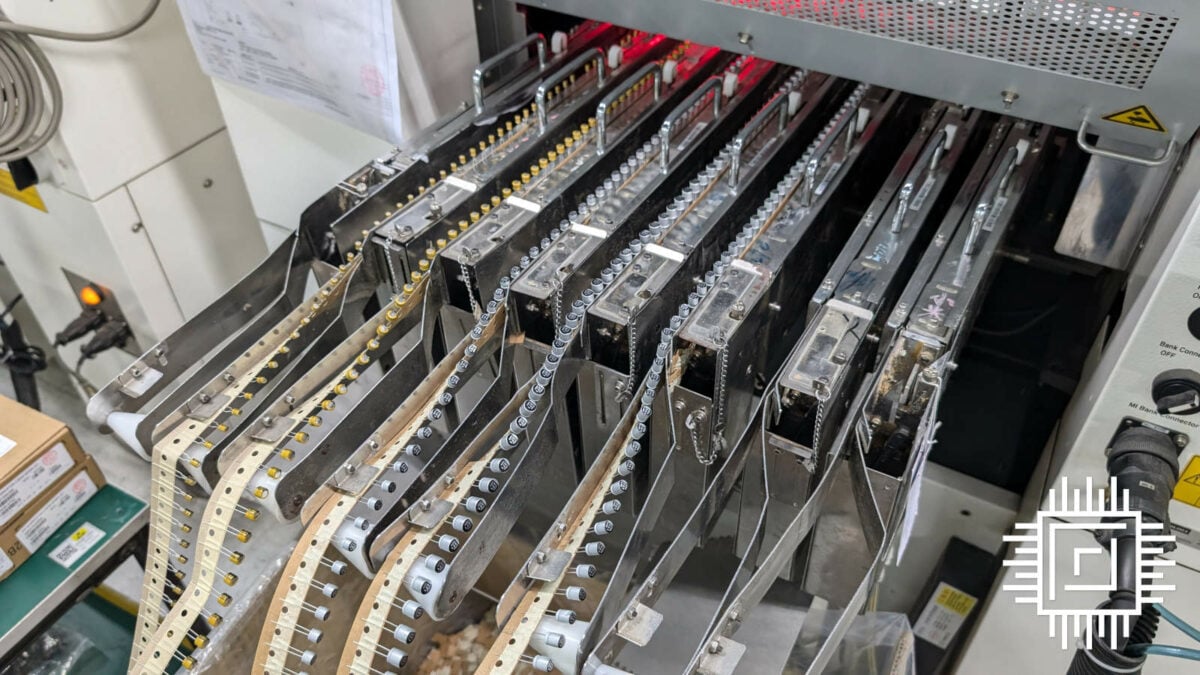
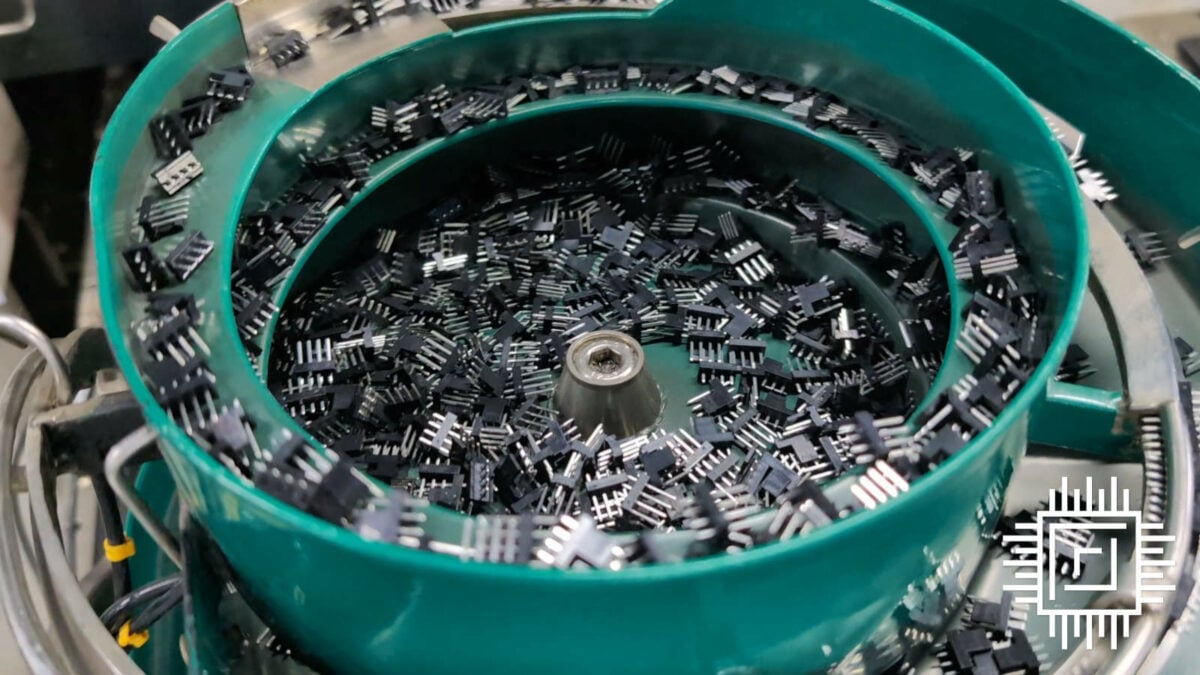
The motherboard is now ready to house the likes of PCIe connectors and PWM headers, but not before it gets a small haircut to trim its PCB down to size. Nobody wants a bloated board, after all. From here, the manufacturing process turns into a miniature carnival of headers, resistors, and more. Pretty piles of pins and ports patiently wait their turn to become part of a greater whole, slowly making their way down a large green slide into the darkness of an otherwise sealed fitting machine. Finally, an AOI will make sure all’s well before the board continues on its journey down the line.
A motherboard every two seconds
There was a time where around 20 operators would manually place connectors on the motherboard, but machines with helter-skelter-like appendages now take their place. Yang shares that this factory employed 12,000 operators at its peak but now only requires 3,000 thanks to innovations in automation. MSI plans to go even further in the next few years, making its manufacturing process entirely automated. If this conjures images of Skynet in your mind, you’re not alone.
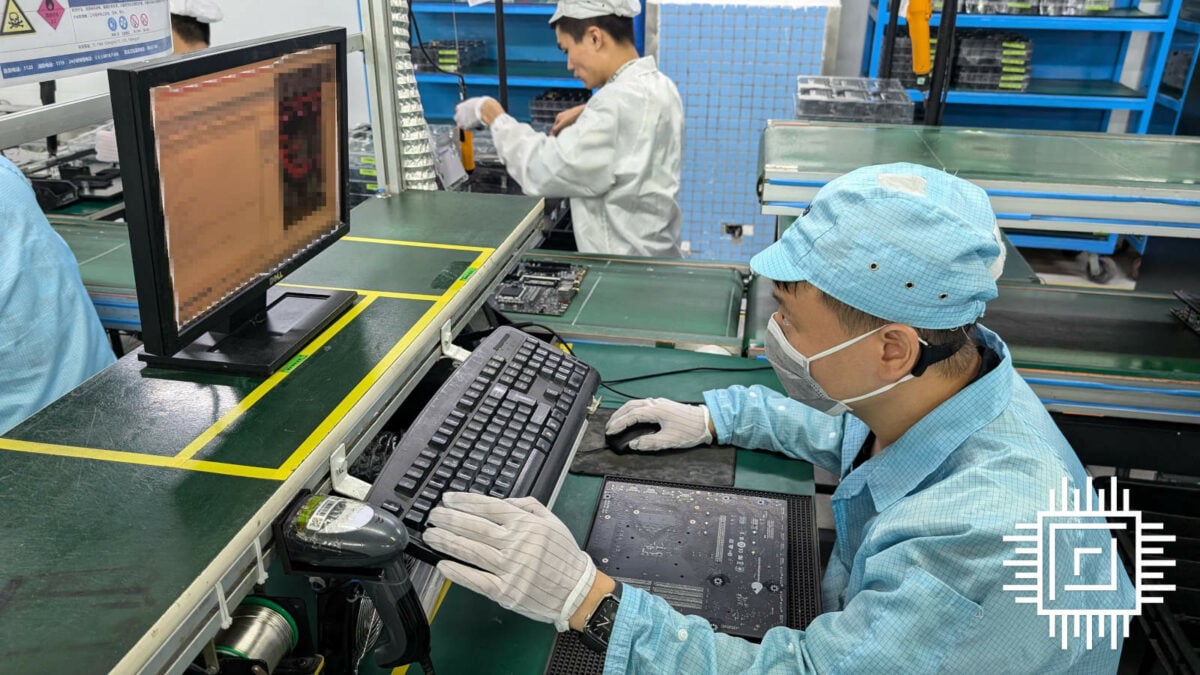
Money isn’t the only driving factor behind MSI’s desire to switch to a fully automated production line. The removal of the human hand in these proceedings should see the quality of motherboards continue to improve, parallel to a decline in retail prices. While this sounds positive, the proof will of course be in the delivery of these promises. Still, if it makes boards more affordable or I can get an MEG Godlike without breaking the bank then I’m all ears.
Returning back to the board, it’s time to solder the newly placed components. Of course, a machine handles this task, with another machine, an AOI, checking over its handiwork. However, if there are any issues then it’s up to a pair of human hands to address any shortcomings. Rather than stand idly by and wait for an on-screen notification, though, the operator receives a push notification to their phone directing them to this particular part of the line. Seeing the software in action, it takes just a few seconds for someone to appear. Impressive stuff.
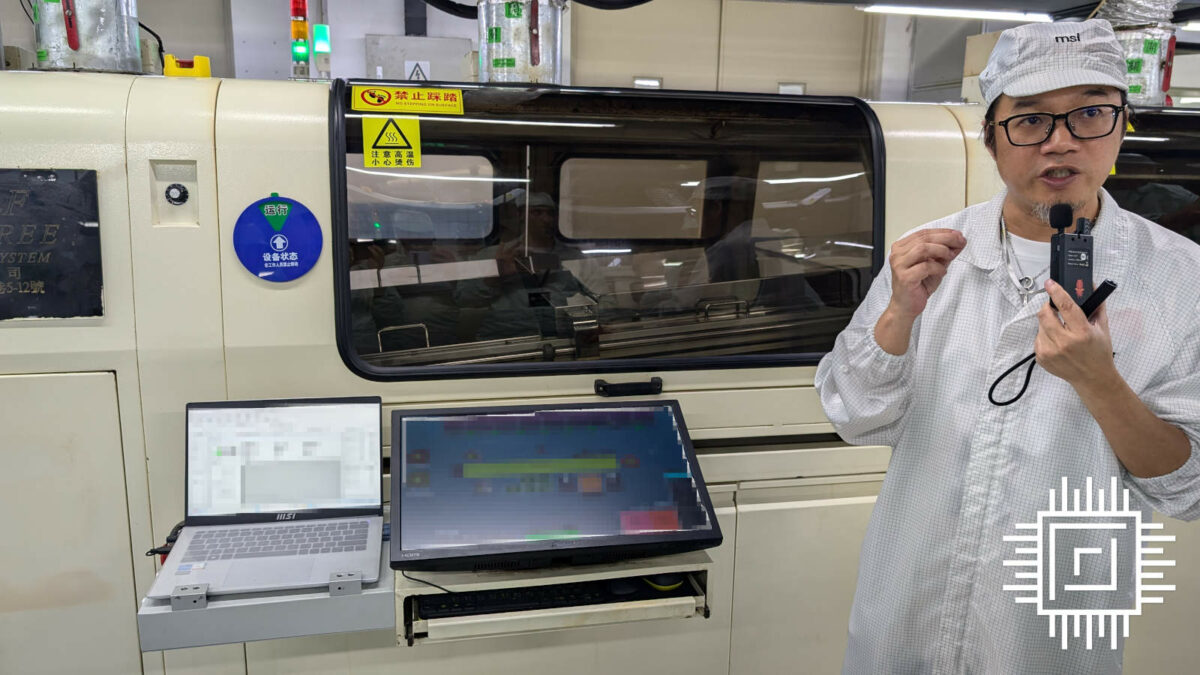
If you’ve ever worked with solder, you’ll know that it can create quite a mess. Naturally, with so much on the motherboard, it receives a thorough clean before the majority of the manufacturing process comes to an end. As you might expect, MSI deploys an AOI to inspect the board after this step to ensure the cleaning stage didn’t cause any damage. Finally, a large robot arm in a cage will test the motherboard’s circuits, ensuring all are open or closed as expected before chipset labelling and the like completes the reign of robots on the line.
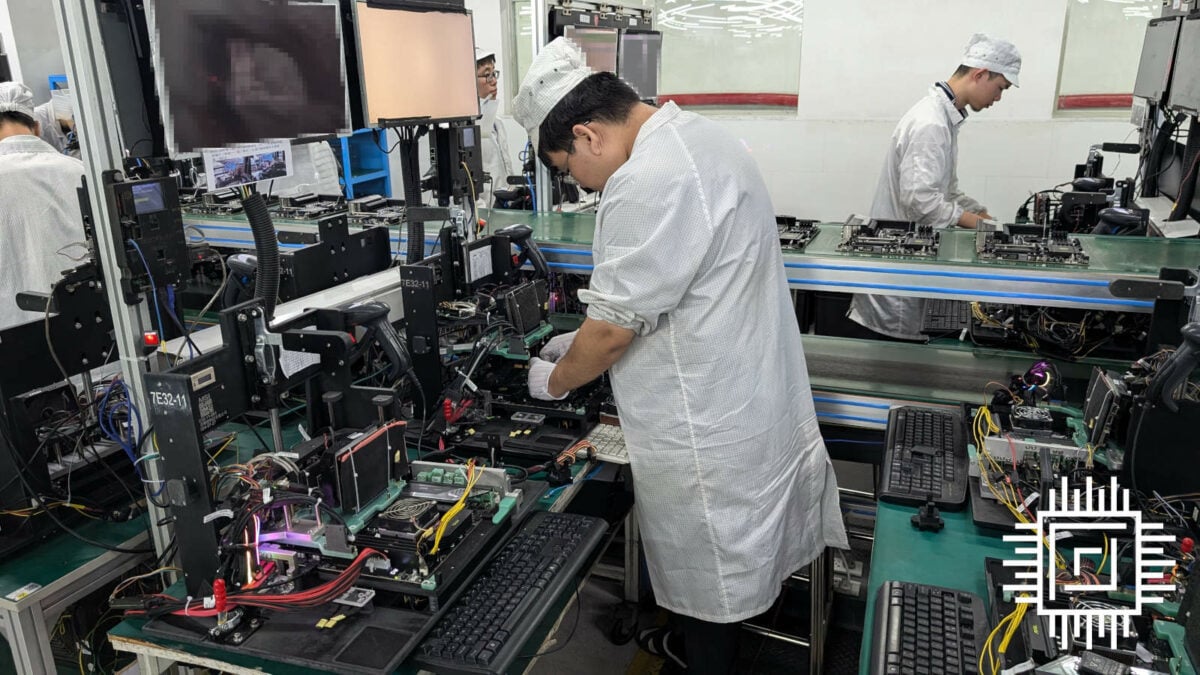
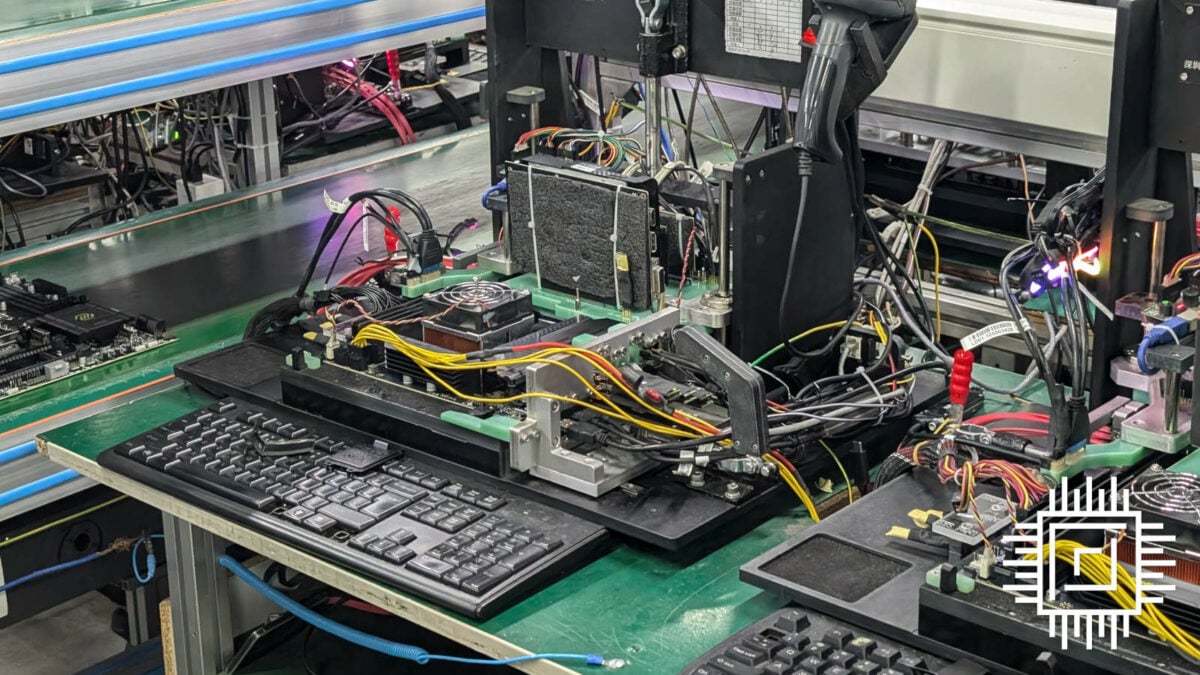
A few steps further and we enter the function-testing stage. As someone that makes full use of their motherboard, always wishing I had more USBs, it pleases me to see MSI stuffing its products with components in every way it can. Operators check every RAM, M.2, and other slot you can think of, as they surround themselves with up to eight systems at a time.
Testing time
Much as humans are necessary to populate the motherboard, a computer handles the functional testing automatically. All the operators need do is load and unload the systems. This approach naturally creates less room for human error, bar during the loading and unloading process. Given how frustrating it can be to diagnose an error on a board, even with debug lights, I wish I could get my hands on this tech.
Before board meets box, it goes through two final checks by AOIs. The first conducts a general spot check of the motherboard, while the last will zoom in on the CPU socket. Here, it’ll take just two seconds to verify the integrity of each pin. As a reminder, Socket AM5 has 1,718 pins, so that’s 859 checks per second. Certainly puts my previous magnifying glass repair acts to shame.
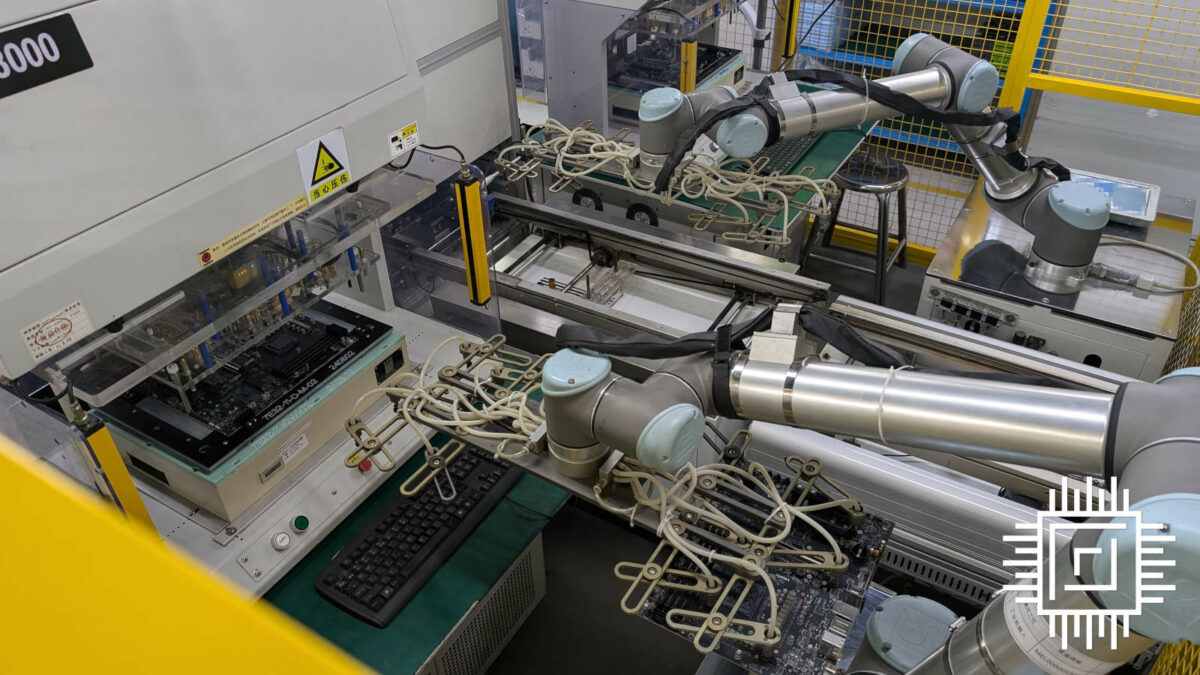
We’re almost at the end of the line, as operators package up the motherboard and its accessories. Scales are present every step of the way to ensure every addition, however small, makes it into the box, right down to that thimble of an M.2 screw. To further ensure quality, however, MSI conducts outgoing quality audits (OQAs). These involve periodically opening sealed boxes, mimicking the customer experience to ensure all is as it should be.
End of the line
And there you have it, that’s how a plain PCB becomes the foundation of your PC. Yang tells me the process is practically identical between AMD and Intel motherboards, save for the function testing owing to the differences in supported formats – Thunderbolt 4, for example. So, all you’ve read above should apply to the board in your system, particularly if it’s from MSI.
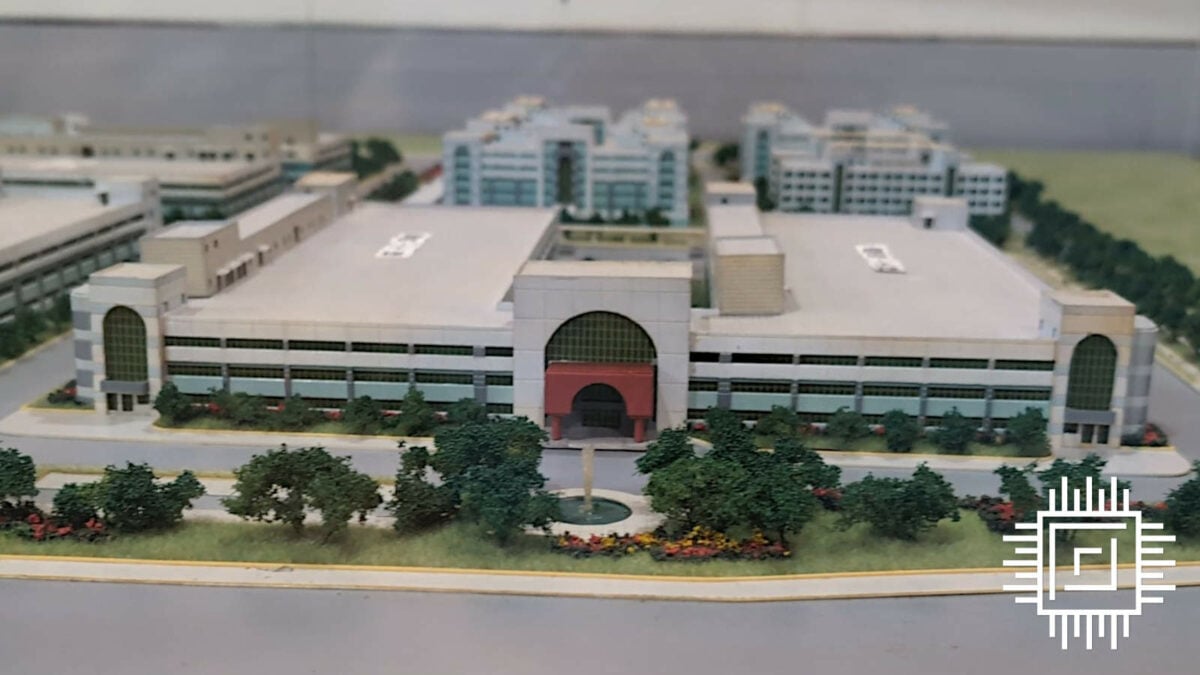
Experiencing the sights and sounds of the production line has given me a newfound respect for motherboards and their manufacturers. Hopefully my descriptions and images above will instil similar feelings, and perhaps a little excitement for chipsets and boards to come.
As we prepare for the launch of Intel Core Ultra 2 series processors, complete with new socket and chipsets, be sure to stay tuned for coverage at Club386. That’s not forgetting AMD’s 800 series motherboards either, which should launch imminently.