The world is changing fast. Nowhere is this more prevalent than in the cutting-edge computing space that has all eyes firmly fixed on artificial intelligence (AI). Driving up the need for at-scale compute, bespoke infrastructure, and putting serious strain on global electricity, AI is here to stay. According to most experts, expect some level of AI in almost every device built from now on.
While you may have the first interaction with AI in the form of generative content from the likes of OpenAI’s ChatGPT, Google’s Gemini, and Microsoft’s Copilot, it’s fast encroaching everywhere. Your smartphone, TV, and even humble fridge either has AI smarts or will have soon, so it’s no reach to consider the technology as an inflection point. AI will touch practically every life in the next ten years, if not sooner.
Companies specialising in building computing hardware have realised serious sales potential and pivoted to include specific AI processing in their upcoming processors. It’s not good enough to merely release a consumer or even server chip that’s marginally faster than its predecessor at general compute. If it lacks robust AI, it’s already lost the best CPU race, as customers will start to look elsewhere.
Huge Demand
As with any nascent technology, AI-infused chips will undergo many iterations, from myriad companies, before we see the best from them. Alongside the obvious hardware, optimised software is required to translate large-language models (LLMs) – the building blocks of AI – into something coherent you can hear or read. Joe Average doesn’t really care about how ChatGPT goes about answering your questions in a human-like way, or the clever programming behind text-to-visual programs such as Stable Diffusion; rather, they care that everything gets better and more intuitive over time. They buy on experiences rather than metrics such as tokens per second.
Evolution happens when many companies work at the AI opportunity through different lenses. Some build for it at frankly ridiculous scale, others work on small-scale AI that’s run on a local computer or, say, smartphone. The one theme that connects them all is that the underlying AI hardware needs to be built in timely fashion via companies with globalised, resilient manufacturing capabilities.
AI is profoundly transforming the world and how we think about technology and the silicon that powers it.
Pat Gelsinger, Intel CEO.
Underscoring this once-a-generation opportunity, the most recent research from respected management consultants McKinsey reckons the total semiconductor industry was worth an aggregate $520 billion in 2023. With AI set to turbocharge production through heightened demand, McKinsey believes the market will explode to over $1tn by 2030. That near-doubling in seven years is music to the ears of semiconductor manufacturers, and this is where Intel hopes to lead the way.
CEO Pat Gelsinger has gone on record in saying “AI is profoundly transforming the world and how we think about technology and the silicon that powers it. This is creating an unprecedented opportunity for the world’s most innovative chip designers and for Intel Foundry, the world’s first systems foundry for the AI era. Together, we can create new markets and revolutionize how the world uses technology to improve people’s lives.”
Incredible Opportunity
But continued consolidation in the at-scale silicon manufacturing space means there are only a handful of companies who have the technology and resources to build the next generation of omnipresent AI hardware. You can literally count them on one hand, with Intel, TSMC, and Samsung leading the way, following by a glut of smaller fabs that now specialise in building chips on older, more established processes. The latest AI superchips carry over 200 billion transistors, so only the most cutting-edge silicon will do. Any company wanting AI infrastructure has, by definition, limited choice. Therein lies massive opportunity.
The prime reason as to why there are so few companies in this sphere is down to the incredible levels of investment required to nurture the most advanced manufacturing processes, and this cost is only going up every generation. Intel, for example, now estimates that a brand-new fabrication facility equipped with the latest EUV lithography technology costs well in excess of $20 billion. At its core, huge opportunity meets significant financial risk.
Intel is unique insofar as it designs a wide range of computer processors for the enterprise, cloud, client, mobile and AI markets and generally builds and packages them across a number of company-run global sites. Other high-profile technology companies such as Nvidia, Qualcomm, AMD, et al, run what is known as a fabless model where in-house design is physically built by a third-party foundry.
This distinction is imperative in understanding Intel’s forthcoming plans. It will continue to build its own products that you are familiar with, such as Xeon, Core, or Arc, but is ready with open arms for fabless companies requiring proven manufacturing capability at practically any scale. The latter becomes especially important in the face of the explosive AI boom the industry is currently experiencing.
Pat’s Plan
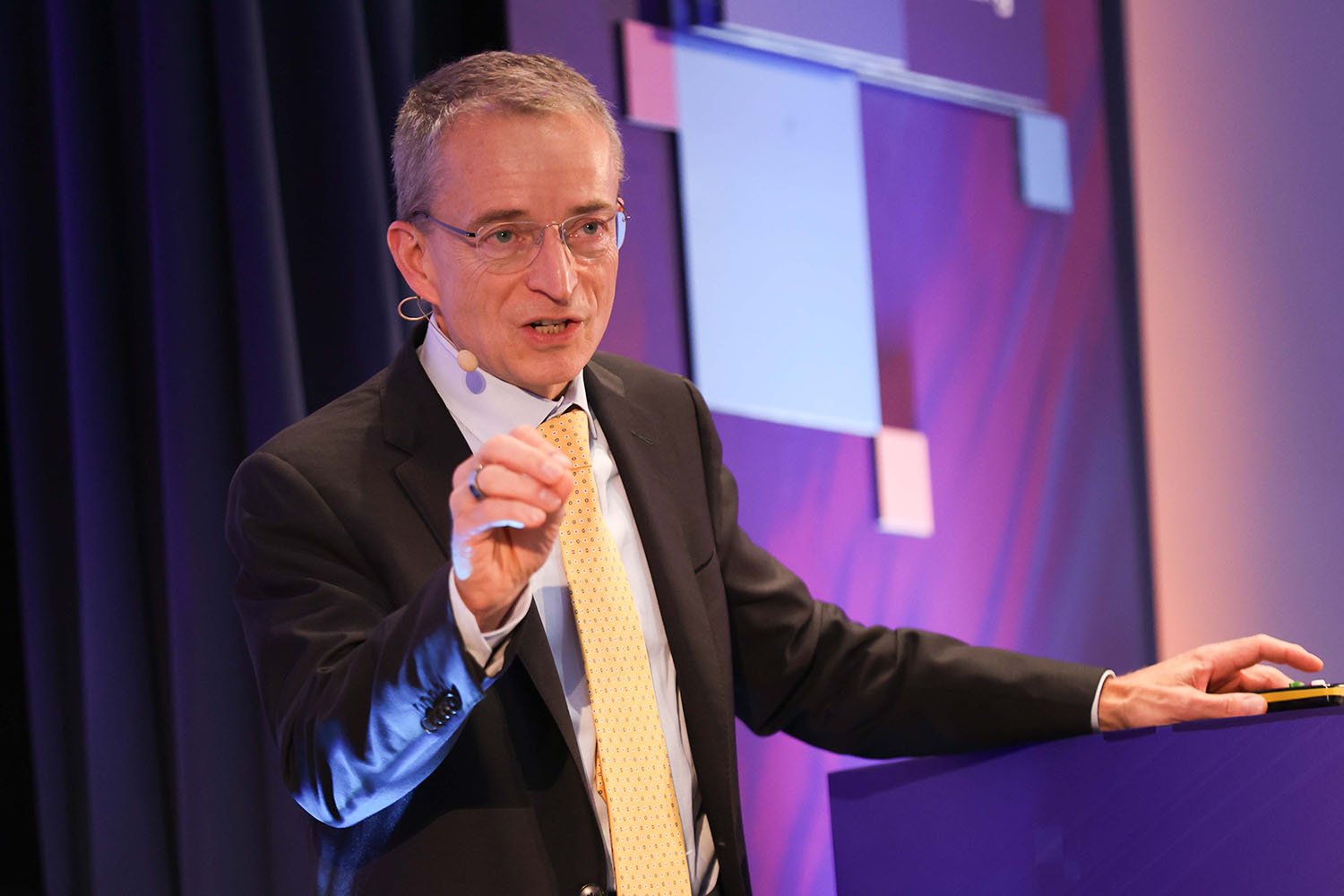
This design and manufacturing duality is the cornerstone of the strategic vision embodied by Pat Gelsinger. Even before the massive AI hardware opportunity arrived on the horizon, Gelsinger has vociferously championed what is known as the Integrated Device Manufacturer (IDM) 2.0 approach.
The three-pillar plan requires Intel to invest heavily into leading-edge processes and manufacturing capability; be nimble enough to use other foundries if and when their technologies make more sense for particular Intel products; and, most pertinently for this discussion, to become a world-class foundry service for fabless customers looking to build the most complex chips. The goal is lofty, with Gelsinger openly stating Intel wants to become the number two global foundry business by 2030.
Make no mistake, IDM 2.0 is arguably the biggest strategic change within Intel since its inception over 50 years ago. The direction effectively splits the company into design and manufacturing arms, each with their own profit and loss accounts, wherein the design group – responsible for products such as Xeon and Core – becomes a customer of the foundry side of the business, paying a fair market price, in the same way Microsoft or Arm is a customer.
In the future, the company will report results from Foundry as a separate operating unit, whereas Client Computing Group, Data Center and AI, and Network and Edge (NEX) results will be filed under Intel Products Group. Accountability and reportability are paramount.
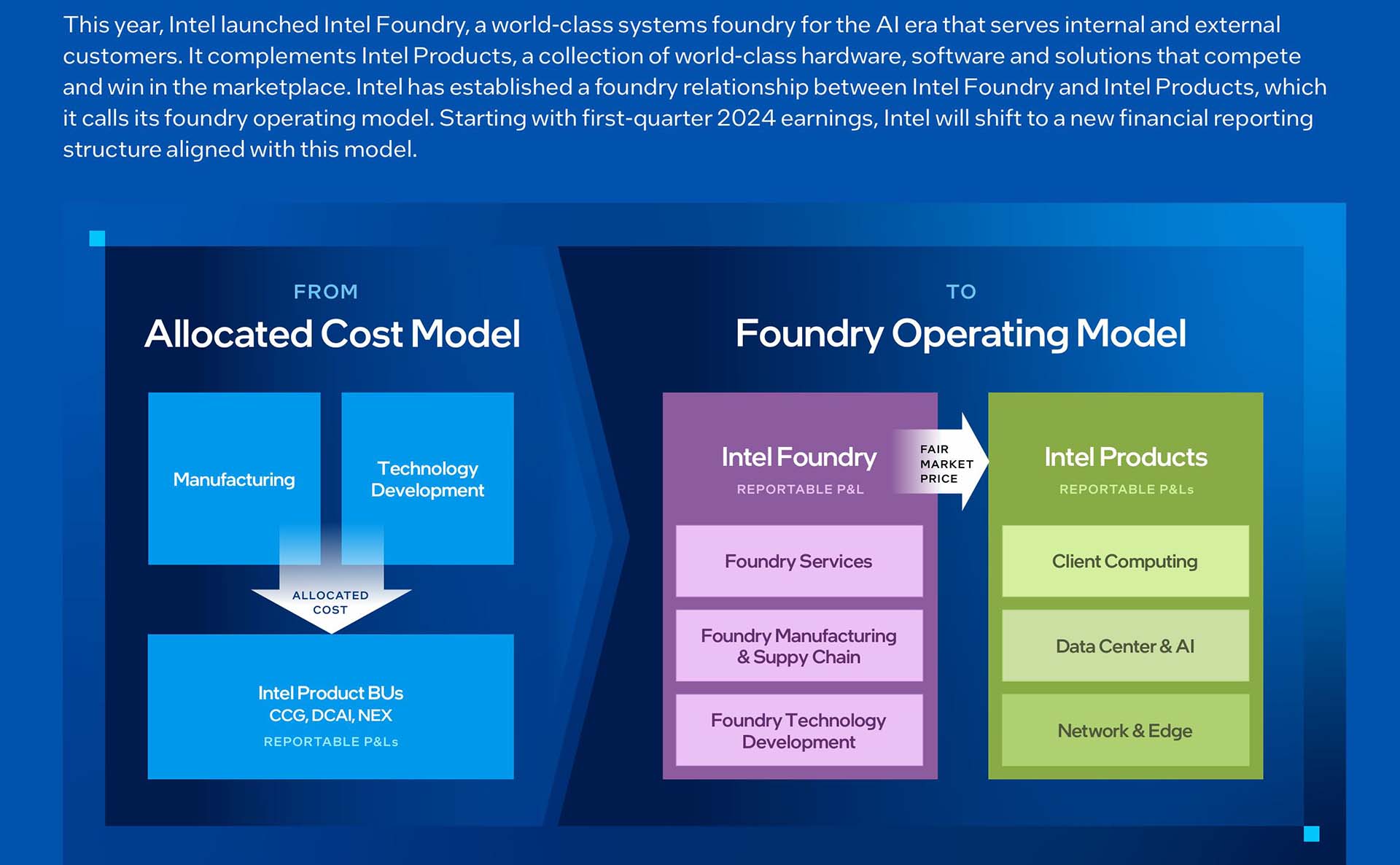
Ramifications are profound. Though I fully expect the majority of Intel Products to be built with Intel Foundry, there may come a time when it’s not expedient to do so. In that case, a particular Core or Xeon may be physically built using technology from foundries such as TSMC.
The notion is hardly far-fetched because a number of current and upcoming high-profile Intel products use some form of manufacturing technology from rivals. Today’s Meteor Lake processors, productised as Intel Core Ultra, carry GPU, SoC, and IO Tiles built by TSMC. In effect, the new strategy dictates that Intel use the most appropriate and timely silicon for its products, whether that by from Intel Foundry or others. Think of Intel as two companies in one.
Why Trust Intel?
Intel’s pivot into offering foundry capabilities as a fully-baked service is a sensible move that has the ability to raise significant revenue in the long term, but it also poses interesting questions. The first and most important is why should any fabless company with key technology trust Intel to build their chips at the requisite complexity and scale? Many of these companies have long-standing ties with established foundries such as TSMC or Samsung, meaning considering porting over to Intel is an inherent risk.
The answer takes a few forms. Fabless customers evaluate many factors before contemplating which foundry to use. Their very existence relies upon taking in-house design and ensuring high-quality silicon comes out at the other end, exactly when they want it to. They need a potential foundry to do many things: instilling utter confidence in a multi-year roadmap they can implicitly trust, having the best packaging technology required for complex chips, and global resilience should a certain fabrication facility not meet the required standards. Beset by recent stalls in technology leadership, Intel has a lot of convincing to do, but it’s on the right path to do so.
Roadmap Execution
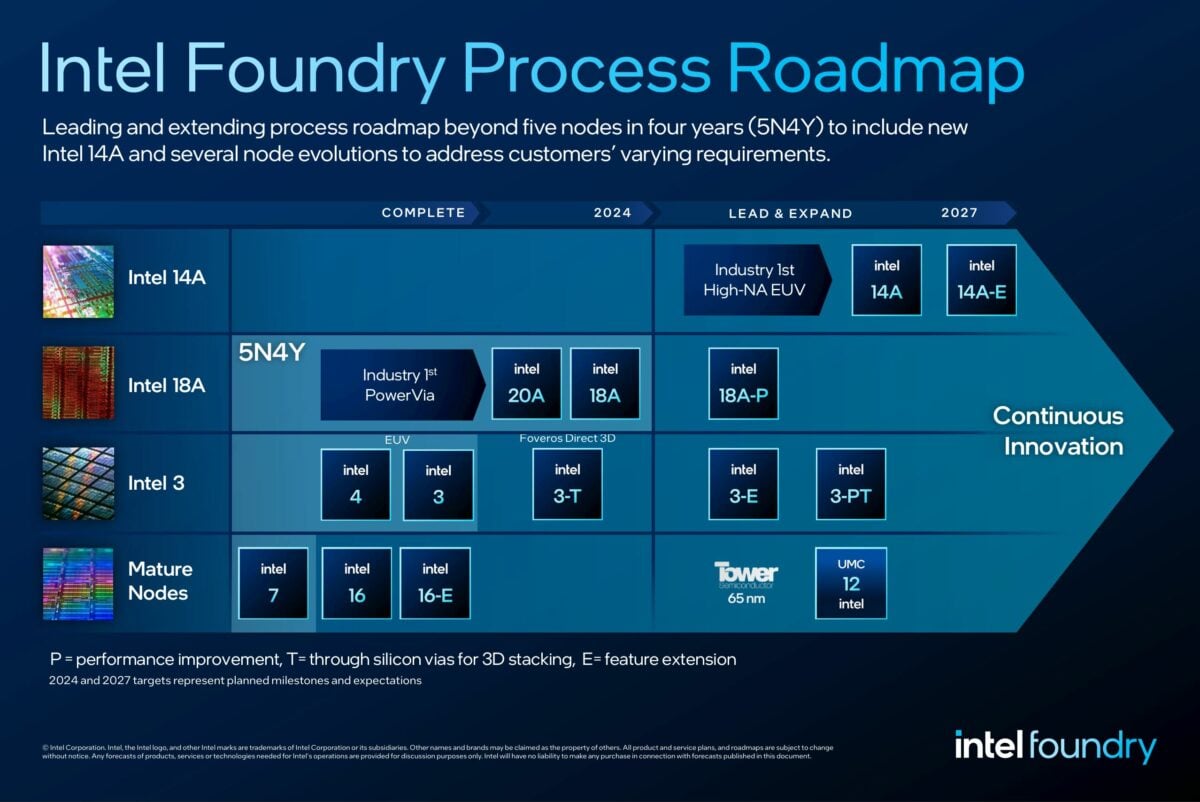
Knowing that manufacturing capabilities fell behind its biggest rivals, Intel embarked on an ambitious project to deliver five process nodes in four years, known as 5N4Y. Depending upon how nodes are defined, achieving this aim requires Intel to launch an 18A product by 2025. The first product to feature this technology are the Xeon Clearwater Forest and Core Ultra Panther Lake processors still on track for next year.
By demonstrating that it can stick to a rapid cadence that requires significant technological innovation at each step, Intel is building goodwill and capital amongst fabless companies. Each node typically offers a double-digit gain in either efficiency or overall performance, and these are the most important metrics for companies looking to build the very best and most complex chips for high-intensity work typically prevalent in AI training and inferencing.
It’s not simply a matter of reducing nodes as a matter of natural course. As we approach smaller and smaller processes, key technological breakthroughs are required to facilitate the smooth movement from one to the next. This makes sense as the circuitry is placed closer together. Intel 4, for example, fits in around 160 million transistors for each mm². Think about that for a second and prepare to have your mind boggled.
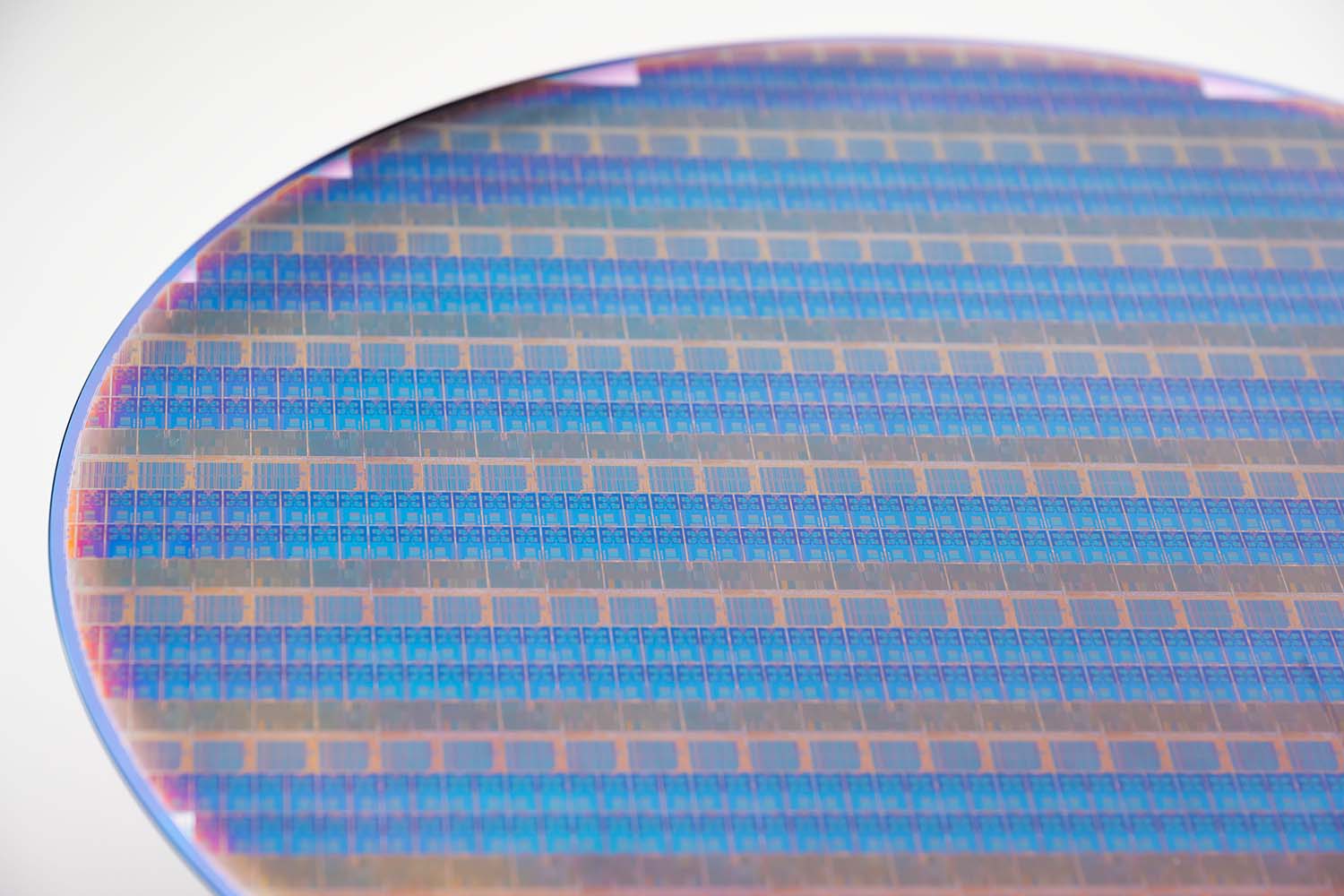
With such proximity, the traditional power and signal wires within a chip become problematic because there’s inherent resistance and interference associated with scale. Simply shifting to a smaller, more-efficient node isn’t possible because other factors like these come into play.
Intel’s solution to this dilemma is backside power delivery known as PowerVia. Though it sounds trivial, separating the power and signal wires by routing the former to the back of the chip not vastly reduces interference but has the added benefit of increasing performance, reducing manufacturing cost, and with some of the wiring at the back, offers more die space for performance-producing transistors. PowerVia is a key reason why Intel’s able to bring in 20A and 18A processes in a timely manner. It’s not magic, but it’s close.
“PowerVia is a major milestone in our aggressive ‘five nodes in four years’ strategy.”
Ben Sell, Intel vice president of Technology Development
“PowerVia is a major milestone in our aggressive ‘five nodes in four years’ strategy and on our path to achieving a trillion transistors in a package in 2030. Using a trial process node and subsequent test chip enabled us to de-risk backside power for our leading process nodes, placing Intel a node ahead of competitors in bringing backside power delivery to market,” according to Ben Sell, Intel vice president of Technology Development.
The ability to churn out volume on 20A and 18A is absolutely fundamental in enticing potential fabless customers to the Intel Foundry fold. Having lagged behind main rival TSMC in manufacturing capabilities for some time, Intel believes the breakthroughs enabling rapid adoption of 20A and 18A bring the company at least level with TSMC for building high-performance and high-value chips typically used in the datacentre and AI spaces, if not ahead.
Underscoring confidence in the future, Intel’s revealed that 75% of the fifty or so Foundry customer test chips are based on the 18A process. The salient point here is if that many would-be customers have been convinced at this early stage, the underlying technology is necessarily robust.
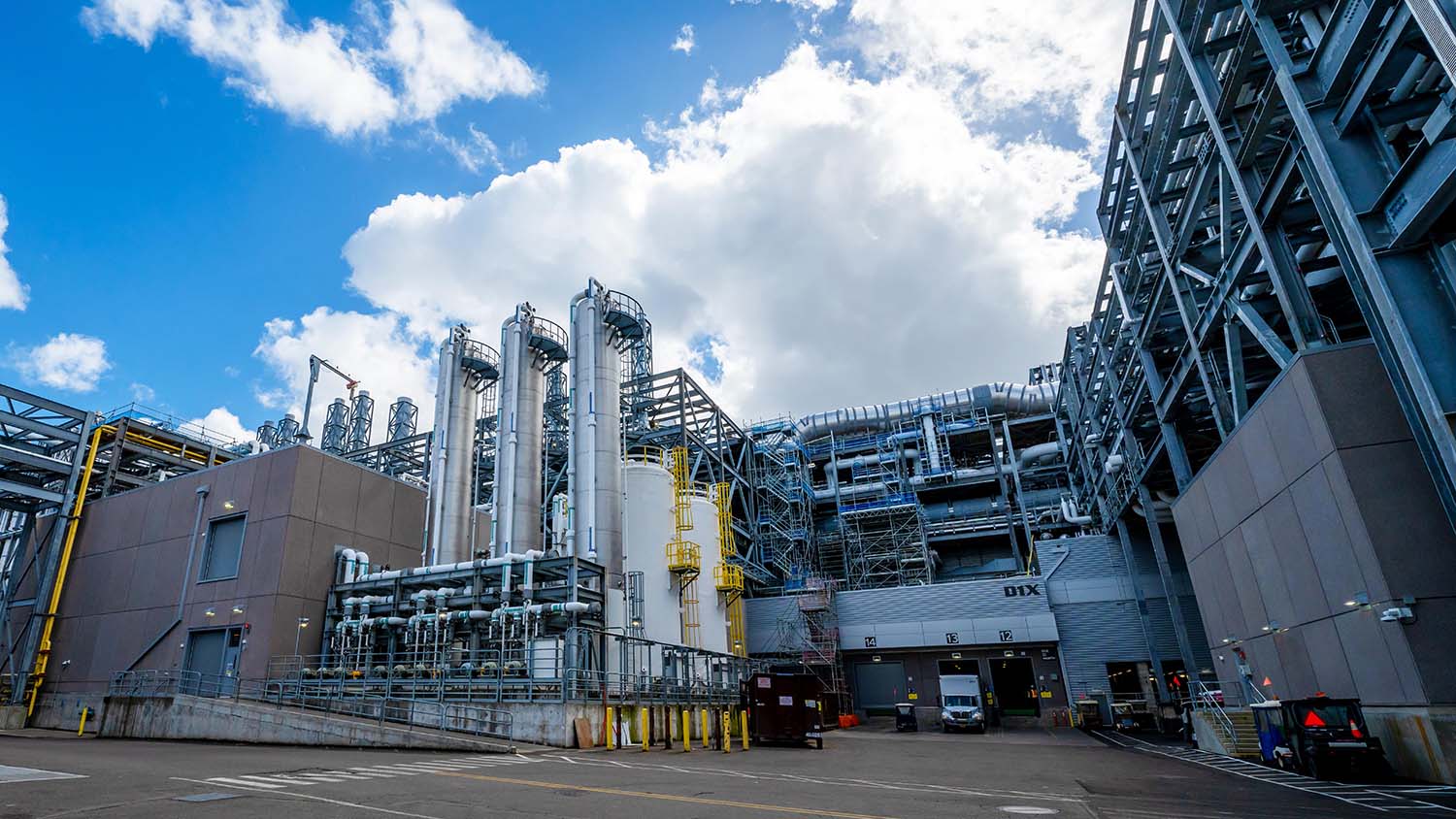
Peering further ahead, other key technologies are on the horizon. Intel Foundry will be the first to use High-NA EUV lithography scanners for the next generation of processors. The industry understands that traditional chip-printing techniques start to become unfeasible for mass production as we enter the 1nm era. Current lasers are simply not precise enough for the task at hand, so a radical solution is required.
High-NA EUV lithography is one answer that Intel’s literally banking upon. Building an EUV-compatible fabrication facility is no small potatoes, mind, as the cost runs into tens of billions of dollars, meaning huge capital bets need placing now. Intel’s already announced that the D1X Fabrication in Oregon now features an assembled EUV machine, ready for 14A and 14A-E in the near future. The company hopes High-NA EUV is a silver bullet in leapfrogging rivals.
To be frank, this acceleration of investment comes on the back of poor decisions in the past. For example, Intel suffered a $7 billion operating loss for the manufacturing unit in 2023, on the back of $5.2 billion a year earlier. The company admits that 2024’s financials will be even worse. Yet there are budding signs of hope and expectation. “In the post EUV era, we see that we’re very competitive now on price, performance and back to leadership. And in the pre-EUV era we carried a lot of costs and were uncompetitive,” said Pat Gelsinger.
Looking through the lens of the present and future roadmap, Intel Foundry’s ability to build leading-edge silicon now appears healthy. Yet no company lives in a vacuum in this space. Many need to come together to help piece together next-generation silicon. Intellectual property and electronic design automation (EDA) partners Synopsys, Cadence, Siemens, Ansys, Lorentz and Keysight have disclosed tool qualification and IP readiness to enable foundry customers to accelerate advanced chip designs on Intel 18A, which offers the foundry industry’s first backside power solution.
Packaging
Fabricating class-leading chips is not the sole preserve of an attractive silicon roadmap. The sheer complexity of modern processors, especially those geared towards heavy-duty AI workloads, oftentimes requires advanced packaging techniques. This is an area where Intel has spent considerable resource for its own products, and technologies such as Embedded Multi-Die Interconnect Bridge (EMIB) and 3D Foveros have proved critical in developing powerful processors.
The reason is it makes little sense for companies to build larger and larger single-chip solutions. Issues such as scaling, defect density, reticule limit, amongst others, preclude single slabs of silicon exceeding 700mm². Rather, firms designing complex processors now rely on tying together multiple smaller processors to act as one. The glue connecting them is packaging. Let me be blunt: without advanced packaging, there are no monster AI chips.
Chip-to-chip EMIB and die-to-die-stacking 3D Foveros are the not-so-secret weapons that Intel uses to manufacture high-performance chips without unduly adding to overall power and latency. Depending upon a potential Intel Foundry customer’s need, any chip can be built on a particular process, with a set of defined power and performance characteristics, and with almost any level of connectivity… from a single piece of silicon all the way through to a 100-billion-transistor chip using a staggering 47 tiles. The latter is actually present on an Intel Max Series GPU, formerly known by the codename Ponte Vecchio.
Efficient packaging becomes even more key in the future. I believe AI chips designed for 2030 will require orders of magnitude more compute, memory, and networking, lassoed together in seamless fashion. Don’t be surprised to see a trillion-transistor processor equipped with 100 tiles. Any company not at the absolute forefront of packaging runs the very real risk of being left behind the manufacturing arms race. It’s not good enough to have excellence in process nodes; a world-class foundry of the future needs intimate understanding of all the constituent systems that make up a high-performance chip.
…we have a capacity and a geographic footprint that makes us much more diverse than some of the suppliers they work with today.
Mark Gardner, senior director IFS.
The future also holds promise of key Intel-led innovations. Late last year, Intel unveiled plans for industry-leading glass substrate to meet the demands of more powerful compute chips. According to Intel, glass substrates possess superior mechanical, physical and optical properties that allow for more transistors to be connected in a package, providing better scaling and enabling assembly of larger chiplet complexes compared to organic substrates in use today.
“From our Foundry customers, the feedback is, one, that we’re a trusted technology company that has a proven track record in both of standard packaging and advanced packaging,” says Mark Gardner, senior director of Foundry Advanced Packaging with IFS. “And because we have such scale, we have a capacity and a geographic footprint that makes us much more diverse than some of the suppliers they work with today.”
Global Manufacturing Capabilities
Intel is also unique in that it offers the most diversified portfolio of advanced fabrication and packaging facilities around the world, numbering over 20 presently. Pregnant with untapped promise, Intel is investing more than $32 billion to build two new leading-edge chip factories and to modernise an existing fab at its Ocotillo campus in Chandler, Arizona, where it will produce some of the world’s most advanced logic chips. A further $4 billion is being spent on equipping operations at Intel’s Rio Rancho campus in New Mexico for the manufacturing of advanced semiconductor packaging. Talking big numbers again, Intel’s pledged a further $7 billion investment for advanced packaging in Malaysia.
Intel’s Fab 34, located in Leixlip, Ireland, is Europe’s first to use EUV in high-volume chipmaking, on the back of a $18 billion total investment. Then there’s a $25 billion expansion at Kiryat Gat, Israel, primed for equipping the facility for EUV lithography, and $33 billion collectively being spent for a chip plant in Magdeburg, Germany.
These eye-watering amounts of money are necessary to maintain a competitive advantage. The sheer investment audacity is only matched by the possibility of garnering hundreds of billions of revenue.
Foundry Partners
A key benefit of the Intel Foundry model is that it already has, for many years, a design customer that’s been committed to high-volume manufacturing. That customer is Intel itself, whose tens of millions of processors have rolled off various manufacturing lines over the past 50 years.
Most of the heavy lifting required to bring a new process to market occurs in conjunction with the Design Group, giving external customers an imputed level of confidence in the viability of silicon. The previous three years have also shown that Intel can execute on multiple nodes, across disparate product lines, and hit the straps at the right time. In fact, Intel has pulled in time-to-market dates for a number of upcoming products, reinforcing the health of the manufacturing arm.
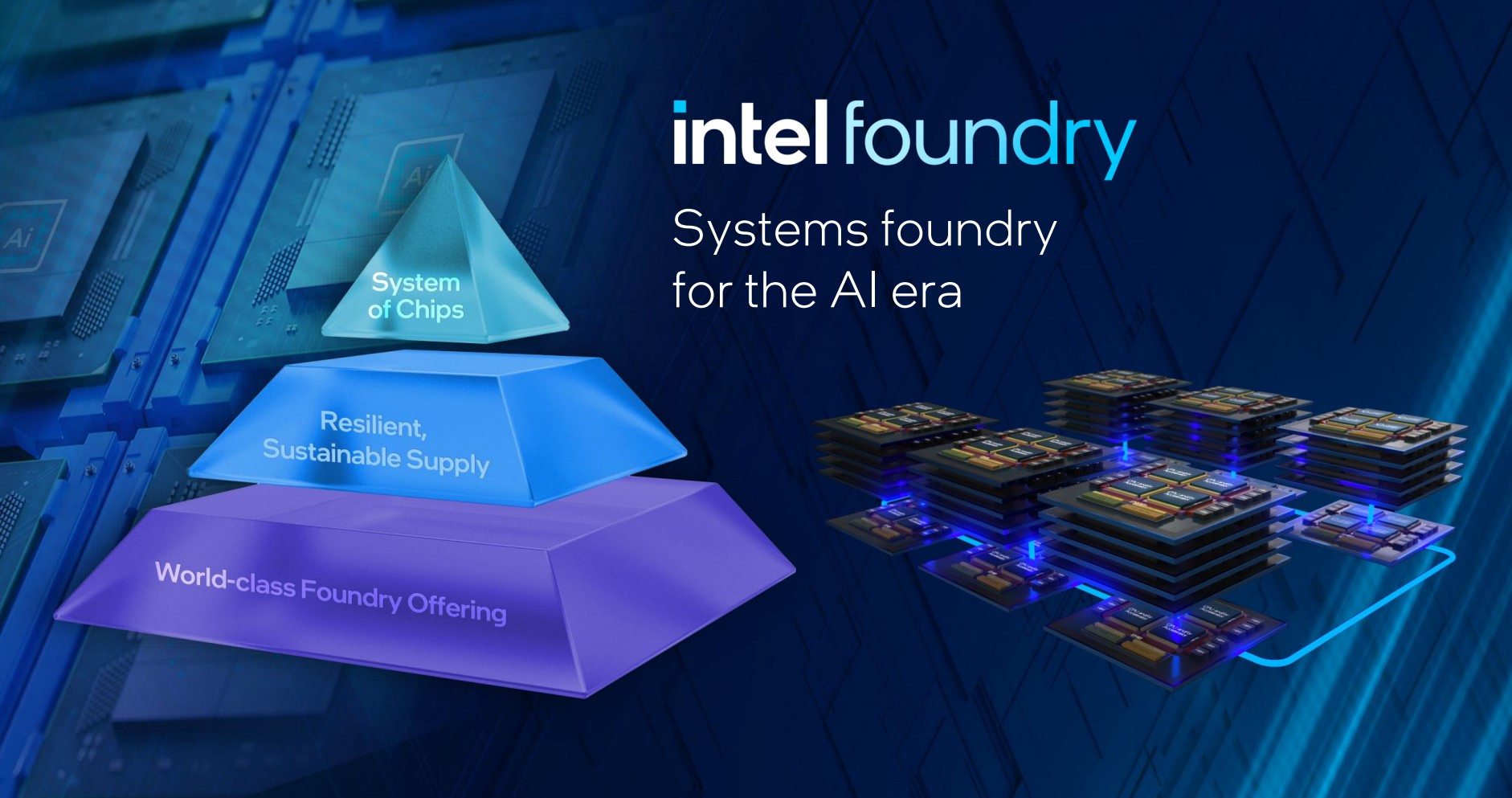
Nevertheless, the Intel Foundry business lives and dies by the number of high-profile customers it can attract. Intel recently announced that Microsoft has chosen the 18A process for an upcoming chip design. “We are in the midst of a very exciting platform shift that will fundamentally transform productivity for every individual organization and the entire industry. To achieve this vision, we need a reliable supply of the most advanced, high-performance and high-quality semiconductors. That’s why we are so excited to work with Intel Foundry, and why we have chosen a chip design that we plan to produce on Intel 18A process,” said Microsoft Chaiman and CEO Satya Nadella. Intel expects this deal to help push the present lifetime deal value of the nascent Foundry business to over $15bn.
Furthermore, Intel and Arm have already announced steps for design technology co-optimisation on future Arm-based cores. Primed for the all-important 18A process, this collaboration ought to make it easier for myriad companies to build their next-generation silicon derived from Intel’s factories. With high-performance Arm designs now successfully infiltrating the datacentre and client markets, ostensibly taking share away from Intel’s x86 offerings, the company puts itself in a position to ameliorate potential losses on the product side with revenue wins on the foundry business.
Not everyone company is in desperate need of the best silicon Intel can produce, however. Some require manufacturing capacity for less complicated chips typically found in networking, IoT, and communications. To this end, Intel has partnered with Tower and UMC, two established foundries with expertise in delivering mature nodes at scale. To be the world’s silicon factory, you need to cater for everyone.
Conclusion
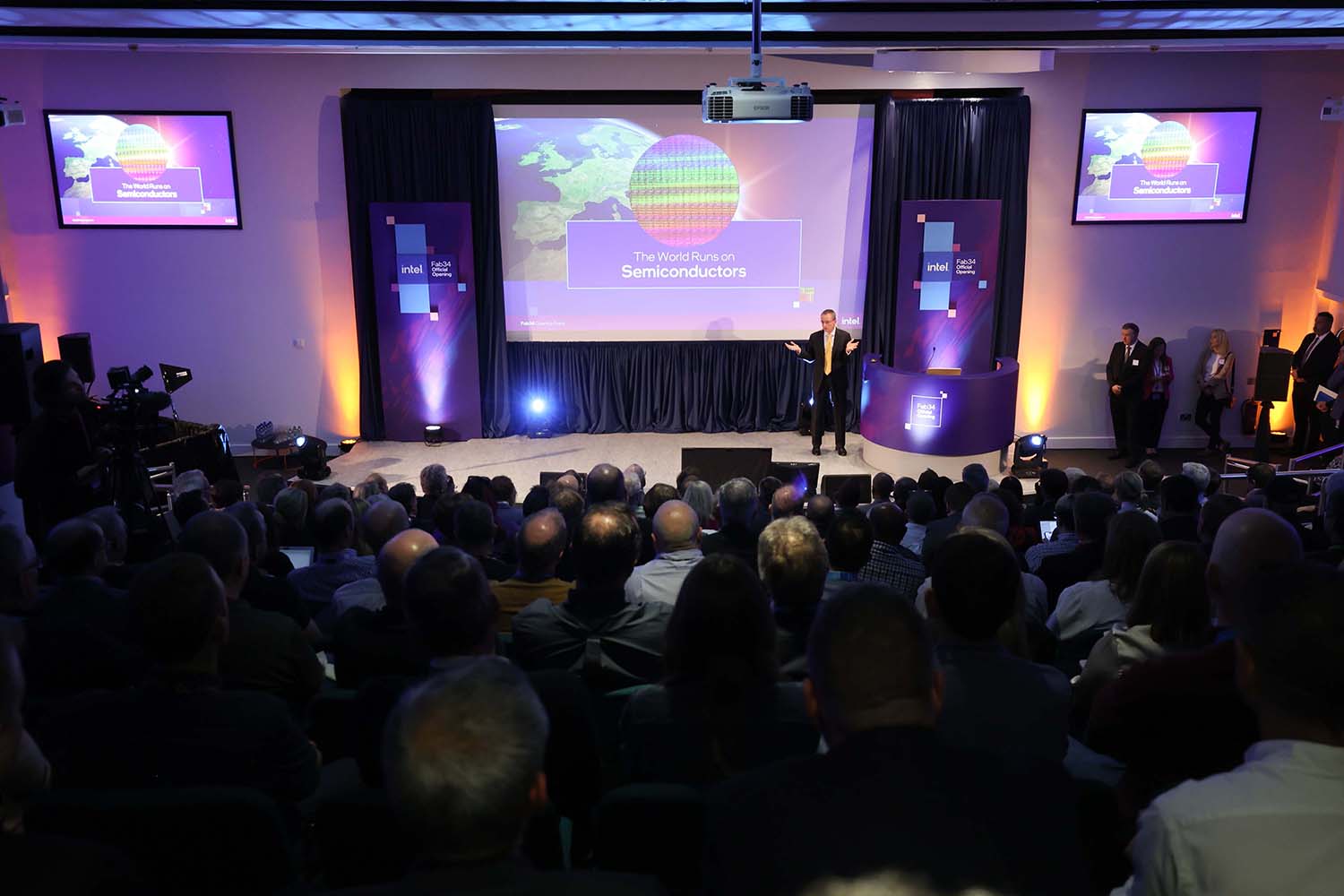
The landscape of chip manufacturing is irrevocably changing. Accelerated by the insatiable demand for AI compute, there’s a global appetite for high-performance chip manufacturing. Previously a company looking inwards, Intel is acutely aware that it can turn one of its key strengths into a future revenue machine that has the ability to become the company’s premier earner. Global foundry services generated sales in excess of $115 billion in 2022, set to double in a decade, and Intel wants in.
This is precisely why Intel Foundry is so important. The fortunes of intrinsic products such as Xeon, Core, and Arc may wax and wane, but it’s undeniable that the semiconductor industry needs cutting-edge manufacturing capacity that’s currently struggling to keep up with demand.
Intel’s bold claim of becoming the number two foundry in the world by 2030 is bolstered by the pieces being assembled on the chessboard under the stewardship of Pat Gelsinger. The process roadmap carries an ambitiousness that is plain to see, promising technology leadership in the not-too-distant future. The packaging arm is just as important in providing potential customers flexibility and choice, while a systems-led approach is the only sensible way to go when building eclectic silicon for yourself and others.
Technology aside, the real proof of any foundry business is in attracting the very best companies. There are none larger than Microsoft, whose upcoming collaboration on the 18A process is the affirmation Intel seeks. Assuming the promise of 18A holds true, I believe Microsoft will be one of many on the Intel Foundry order books.